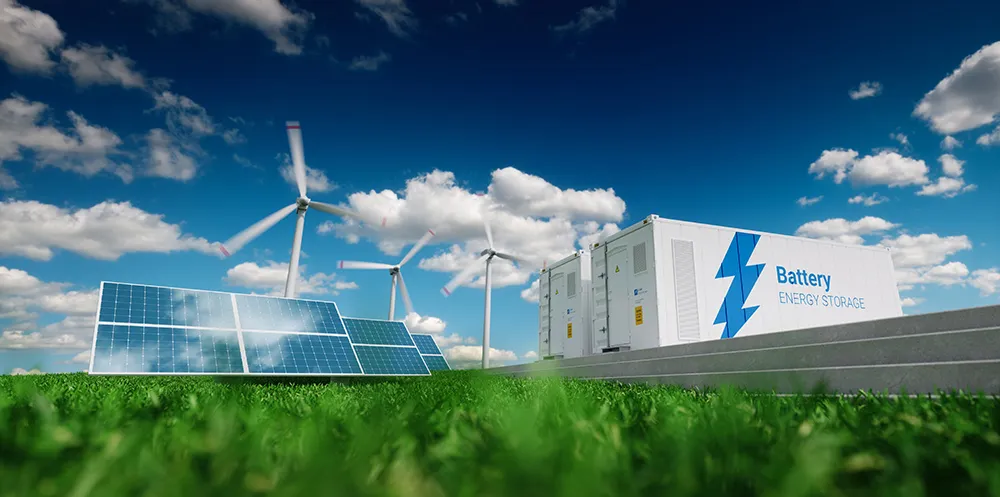
Plastic Innovation Sails Renewable Energy Transition
Amid the global shift toward low-carbon energy and the continuous optimization of energy consumption structures, the demand for renewable energy is steadily increasing. Meanwhile, the rapid development of the new energy industry is driving higher performance requirements for materials.
High-performance polymer materials and thermoplastic composites, with their advantages of lightweight, weather resistance, design flexibility, and cost-effectiveness, have become core supports in segments such as photovoltaics, marine and wind energy, and hydrogen energy.
Source: Adsale Plastics Network (www.AdsaleCPRJ.com)
The latest report from the International Energy Agency (IEA) indicates that between 2024 and 2030, global renewable energy capacity additions will exceed 5,500 GW, with photovoltaics accounting for 80% of the increase, primarily driven by the construction of multiple large-scale solar and rooftop solar projects.
TrendForce, an international market intelligence company, predicts that global photovoltaic installations will reach 596 GW in 2025, a year-on-year increase of 6.0%. As global photovoltaic installations continue to grow, the demand for solar panel components is also surging.
In encapsulant films, backsheets, panels, structural components, and other parts, plastics play a significant role in the development of photovoltaic systems due to their lightweight, low-carbon, and low-cost advantages. In particular, composite materials, with their high strength, corrosion resistance, strong weather resistance, and high energy efficiency, are becoming alternatives to traditional metal materials.
Lightweighting and Decarbonization
In the pursuit of sustainable development, lightweighting and decarbonization have become the keys to the transformation and upgrading of many industries. From transportation to the energy sector, these are not only environmental necessities but also crucial for improving economic efficiency and resource utilization.
BASF's innovative photovoltaic frame integration solution combines polyurethane material frames with water-based coatings, along with engineering plastic corner brackets, providing a more corrosion-resistant, insulating, and lightweight solution for photovoltaic applications. This solution is suitable for photovoltaic applications in the sea, desert, and city. Compared to traditional aluminum frames, this solution can reduce weight by 30% and significantly lower the carbon footprint by 85%.
Weather resistance and low cost
Photovoltaic encapsulant films are key auxiliary materials for encapsulation to protect solar cells. Since photovoltaic modules operate in open environment, photovoltaic encapsulant films need to exhibit excellent resistance to erosion, heat, oxidation, and UV aging under harsh condition. While pursuing high performance, cost reduction has also become an important development direction for the photovoltaic encapsulant film segment.
Wanhua Chemical's WANSUPER® polyolefin elastomer (POE) went into production in 2024. The material can be applied to photovoltaic encapsulant films, providing a light transmittance of >91%, a 20% improvement in weather resistance, compatibility with double-glass module requirements, and a 15% reduction in encapsulation costs.
The Delrin® material used for solar tracker bearings is specifically designed for photovoltaic applications. It can withstand outdoor environments for an extended period and has excellent impact strength, UV resistance, and thermal stability, making it suitable for photovoltaic tracking systems. This ensures that solar panels efficiently track the sun throughout the day.
The Brückner stretch film production line employs advanced stretching technologies, such as LISIM® (Linear Motor Simultaneous Stretching) technology, enabling the production of extremely thin films with thicknesses down to 2.5 microns or even thinner.
Energy efficiency improvement
Enhancing the efficiency of photovoltaic systems through technological innovation has become an crucial pathway to achieving the goals of carbon peaking and carbon neutrality. Beyond component optimization and system integration, material innovation is also becoming a key to break through the efficiency boundary of the photovoltaic segment.
BASF's innovative flame-retardant material portfolio (Ultramid® PA, Ultradur® PBT, and Elastollan® TPU) helps maximize the power generation efficiency of solar panels while ensuring the safety and reliability of the equipment.
SABIC's FORTIFY™ PV POE, suitable for photovoltaic encapsulation materials, has a higher volume resistivity than EVA. The longer the service time, the higher the module power, maintaining low leakage current and ensuring the stable operation of photovoltaic power generation systems to meet growing energy demand.
With the rising global demand for renewable energy, the offshore wind market has shown strong development momentum. According to the Global Wind Energy Council (GWEC), global offshore wind installations are expected to reach 18 GW, 23 GW and 29 GW in 2024, 2025 and 2026, respectively.
As offshore wind energy moves further into deeper water, the demand for longer blades will continue to increase. Developing larger, lighter, and lower-cost wind turbine blades is a key trend for the future. Composite materials, with their advantages of lightweight, high strength, design flexibility, and low cost, have become the materials of choice in the wind energy segment.
Currently, composite materials generally account for more than 90% of the weight of wind turbine blades, with the load-bearing structure composed of glass fiber or carbon fiber composites. These materials feature high strength and low density, effectively reducing blade weight and improving wind energy capture efficiency and operational stability.
China Jushi Co., Ltd. has independently developed large wind turbine blades using E8 and E9 series high-performance glass fiber composites, reducing weight by about 30% and increasing power generation efficiency by about 10%.
On the other hand, since offshore wind equipment is exposed to marine environment for extended periods, some structural components are prone to electrochemical corrosion and stress corrosion cracking. Advanced high-performance polymer materials help improve corrosion resistance and extend the overall lifespan of offshore wind power transmission systems.
Ensinger is a leader in the carbon fiber composite materials market for wind turbine blades. Its products are widely used in the manufacturing of wind turbine blades, contributing to increased strength and durability of the blades.
With the rapid development of hydrogen energy technology, chemical-resistant polymer materials are playing an increasingly vital role in the hydrogen energy field. These materials are widely used in multiple key links, including proton exchange membranes, hydrogen storage tanks, and water electrolysis equipment.
According to the research report of China Association for the Promotion of Industrial Development, the global hydrogen demand is expected to grow tenfold by 2050, with the entire industrial chain's production value exceeding US$2.5 trillion. The development of hydrogen energy presents huge opportunities to the application of polymer materials.
As one of the core components of hydrogen fuel cells, proton exchange membranes (PEM) require high proton conductivity, low gas permeability, and excellent chemical stability.
Chemours, with its deep technical expertise, has been dominating the PEM market with its Nafion® perfluorosulfonic acid (PFSA) membranes. Asahi Kasei's Aciplex™ membrane is a perfluorosulfonic acid proton exchange membrane. Perfluorosulfonic acid offers excellent chemical stability and mechanical strength, allowing it to operate stably in harsh chemical environments, such as strong acids and strong bases, with minimal risk of chemical degradation.
For hydrogen storage tanks, Type IV tanks are entirely made of resin, making them easy to mold. They mainly adopt a plastic liner made from polyamide(PA), lined with CF composite winding. Arkema's bio-based PA11, used in high-pressure hydrogen storage tank liners, offers excellent hydrogen barrier properties, resistance to high-pressure hydrogen bubbling, high and low-temperature resistance, environmental friendliness, and excellent processability.
With the rapid development of renewable energy, high-performance polymer materials and composites play a core supporting role in segments including photovoltaics, wind energy, and hydrogen energy. Material innovation not only drives the upgrading of the new energy industry but also helps advance the global energy structure toward low-carbon and sustainable development.
微信扫一扫:分享
Open WeChat
Scan QR code to share